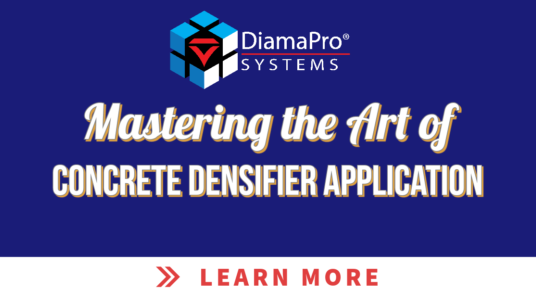
Liquid hardeners/densifiers provide a cost-effective solution to increase the service life of the concrete substrate and enhance its abrasion resistance, reduce surface dusting, and fill in micro pits. It can also be used to “lock” in dyes during the polished concrete process.
Understanding Concrete Densifiers
Concrete is made up of cement, water, and aggregate and at times liquid admixtures to enhance one or more fluid and hardened properties. When water and cement are combined, a chemical reaction immediately starts. This is called cement hydration. During this reactive process, a few new chemicals are produced, calcium silicate hydrate and calcium hydroxide.
Calcium silicate hydrate (C-S-H) is the most important chemical produced during the hydration of Portland cement and is primarily responsible for the strength of cement-based materials (concrete). It is the primary binder ("glue") in concrete holding all the aggregates together.
While calcium silicate hydrate is produced, another chemical is formed, calcium hydroxide. Calcium hydroxide is a byproduct of the cement hydration process and has no value within hardened concrete. Due to its chemistry, it was determined that when you apply a liquid silicate to the surface of a hardened concrete slab, it reacts with calcium hydroxide and produces more calcium silicate hydrate. This reaction, over time, increases abrasion resistance and develops a crystalline structure filling some of the micropores and decreasing surface porosity.
Several types of silicates can be used as a concrete treatment. The three most used are sodium, potassium, and lithium. Sodium and potassium are similar in performance with a few differences.
Lithium or a blended silicate, which contains a combination of more than one, in the polished concrete industry, is what most of the installers will choose, and for good reason. A molecule is very small in size. The lithium molecule is the smallest when compared to the others. Having the smallest molecule has its advantages.
Let’s compare silicate molecule sizes using the ice analogy. Which one will melt faster, a one-pound block of ice or one-pound of cubed ice? The answer is cubed ice. It is based on how much surface area there is with each. The exposed surface area of one pound of cubed ice is much greater than a block. Lithium silicate is smaller. It has a more reactive surface area than a larger silicate molecule. This translates to speed and efficiency. Silicates that contain lithium silicate will have a faster reaction time and a better chance to completely react.
When to Apply Concrete Densifier
There are several reasons why one would use a liquid densifier/hardener, but they all have one thing in common, to increase abrasion resistance of the surface. When concrete cures, about 50% of the water induced during production comes to the top of the slab. Depending on how the concrete was finished when placed, how wet the subgrade was during placement, the ambient temperature and humidity, how much water is in the mix, and how it was cured will impact the abrasion resistance of the concrete surface. Cement needs water to develop the intended strength. With too much or too little water, the strength goes down.
The optimum time to apply a liquid silicate is when the calcium hydroxide has sufficiently developed within the slab. Again, silicates react with calcium hydroxide producing calcium silicate hydrate (glue). Generally, this will be around 28 days after concrete placement. Now, the longer the concrete hydrates, the more calcium hydroxide is produced. This process never ends. For example, the Hoover Dam, which was constructed between 1931 and 1936 and crosses the Colorado River, is still hydrating. Temperature probes have been inserted into the dam checking temperature. The chemical reaction happening during the concrete hydration process will generate heat that is easily measured.
Preparing the Concrete Surface
The concrete substrate needs to be able to absorb the silicate for it to react. If the substrate is absorptive, no matter how old it is, a liquid silicate can be applied and will perform as intended. Some silicates contain surfactant. Surfactants decrease the surface tension of the water in the silicate. By adding a surfactant, the ability for the silicate to absorb is increased.
During the polished concrete process, liquid silicate is usually applied for several reasons. When polishing, having a harder surface is advantageous. Diamond tooling cuts more efficiently when the surface is uniform in hardness. Silicates produce a more uniform concrete surface across the entire floor. Having a uniform hard surface allows the same tooling to be used in the early stages of the polished concrete process. Lastly, silicate will increase the service life of the finished floor. Having a hard, abrasion-resistant, polished floor will provide years of service.
Concrete Densifier Application Process
The application of liquid silicate is quite simple. Using a pump sprayer and microfiber applicator will be all you need. If the area is auto-scrubbed before the application, allow it to dry. The additional water left behind from the auto-scrubber will not compromise the chemical reaction, but it will minimize the penetration into the slab.
Start by generously systematically spraying the material onto the floor. Start in the far corner of the area and work your way out. Make sure the entire area is covered. With the microfiber applicator, move the material from wet areas to dry. This will ensure even coverage. The coverage rate will be around 400 sq.ft./gallon. Silicates are low cost, do not skimp when applying the material.
The material should remain wet looking for 15-20 minutes to obtain full penetration. Moving the wet material from puddled areas to dry areas will provide optimum and even coverage. Once the material has reached full absorption, the surface can be auto-scrubbed or allowed to dry. If allowed to dry, make sure there is minimal to no amount of material on the surface. If there are puddles, the silicate will dry, and a white crystal will remain that needs to be mechanically removed.
Appearance
Silicate is not a coating; it penetrates and chemically reacts with the concrete to harden the surface. The enhanced appearance comes from what steps are taken next. If the slab is to be only cleaned and densified, running a burnisher or auto scrubber over the area multiple times will enhance the gloss. Densified floors react very well to abrasion produced by a high-speed burnisher or auto scrubber fitted with a diamond-impregnated pad. This reaction is not immediate, it happens over time.
When polishing a slab, the process uses diamond tooling. Starting with a coarse grit diamond tool and moving to finer and finer grits provide the visual and physical change to the surface. The silicate does not produce these changes, it hardens the concrete allowing it to be polished.
Maintenance Post Application
Most silicate-hardened floors are maintained using only an auto scrubber. There are cleaning solutions that can be used with these machines. A high-speed burnisher fitted with a diamond-impregnated pad will keep the gloss level like new.
A floor that has been densified is not chemical resistant. The chemical reaction that occurs between the silicate and concrete will not stop the attack of industrial or organic acids (vinegar, orange juice, Coke). If you wish to have protection from these contaminates, an additional topical or penetrating system needs to be applied as the last step.
Conclusion
Although a properly placed, finished, and cured concrete slab is very durable, the performance can be elevated using liquid silicate. Liquid silicates do not form a film, they react with concrete hardening the surface, filling the fine pore structure. They can be used in many environments; anywhere exposed concrete is the traffic bearing surface. If you are interested in increasing the abrasion resistance of your concrete floor, liquid silicate is the most cost-effective method to do so.