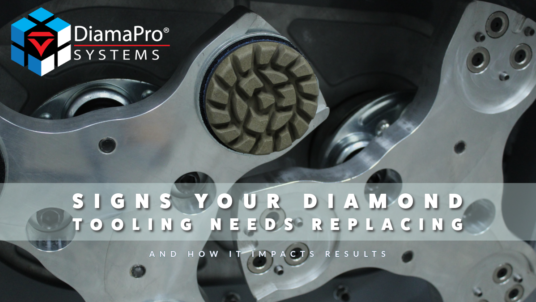
There are many diamond tool suppliers in the grinding industry. There are styles for hard concrete, for soft concrete, and everything in between. The diamond grit size will vary depending on your desired result on a particular concrete surface. Selecting the correct diamond tooling will help you get the project completed earlier and use fewer tools.
Being able to “read” the floor is especially important. When grinding, you not only use your eyes to see what is happening, but you also use your ears to hear how the tools are cutting. You can see how the tooling is cutting by looking behind the grinder. But the sound the correct tool is making is very distinctive. You will also feel the grinder grab the floor while cutting. You can instantly tell how the diamonds are working by how much pull the machine has.
No one type of tooling will perform well on every project, which is why there are so many types. There are ways to determine if the diamond tooling you have selected is right for the floor you are standing on.
Why Diamond Tooling Wears Down
When selecting diamond tools for a project, the hardness of the concrete needs to be determined. The Mohs Hardness of the concrete will provide you a value to work with. The hardness of the concrete correlates to the bond hardness of the diamond tool.
All diamond grinding tools use manufactured industrial diamonds as the abrasive. The abrasive, encapsulated in a ridged or semi-ridged bond material, is adhered to the tool base. As the tool grinds, this bond material wears away exposing new, fresh diamonds. Eventually, a new set of tools will need to be used.
The bonding material that holds the diamonds to the tool comes in different hardnesses. If the incorrect hardness is used, it might compromise the life of the tool and wear at a faster-than-normal rate. The tool bond hardness is directly associated with the hardness of the concrete.
Key Signs Your Tooling Needs Replacing
- Slow Production Rate:
- The production rate correlates to profit. The less efficient the tooling is, the more time you will spend on site.
- Using the incorrect bond hardness will lower the production rate.
- Running the grinder at too high a speed will not allow the diamonds to cut the floor. They could skip across the surface without grabbing.
- Excessive Heat Buildup:
- Generating elevated levels of heat will cause the diamonds to glaze. This is when the diamond becomes encapsulated in the bonding material, reducing the tool’s ability to cut.
- Selecting the correct bond will minimize glazing.
- Grinding wet or at least dampening the slab will help to cool the tooling.
- There are grinder models that have adjustable weights, like the DiamaPro Systems grinders. The weights can apply more head pressure to the tooling causing abnormal friction. Remove the weights or set them in the back position if too much heat is being generated.
- Inconsistent Scratch Pattern:
- Scratches are from the diamond tooling abrasive.
- Not all diamond tools are equal from every manufacturer. Larger diamonds mixed in with smaller ones can cause an irregular scratch pattern. It’s important to select a quality tool manufacturer such as DiamaPro Systems, which ensures uniform diamond sizes in a tool.
- The floor needs to be cleaned after each cut, removing all the spent or broken loose diamonds. They can trap under the grinder scratching the floor when making the next cut.
- The grinder needs to move at a consistent speed across the floor when grinding. If the speed is erratic, you could see an inconsistent scratch pattern.
- Premature Diamond Loss:
- If a soft bond tool is used on soft concrete, the bond will wear away extremely fast, reducing tooling life. Tool bond selection is important.
- Audible Changes:
- When grinding with a metal bond tool, there is a distinctive sound produced.
- The grinding noise should be consistent with each tool.
- If the pitch of the sound lowers, the tools might be too aggressive.
- If the pitch of the sound rises, the tooling might not be cutting as well as it was.
Impacts of Not Replacing Worn or Incorrect Tooling
- Project Delays:
- Incorrect and worn tooling reduces production rates.
- Inefficient grinding extends the time on a project.
- Incorrect tooling requires additional tooling needed in the trailer.
- Incorrect or prematurely worn tooling will require an unwanted trip to your shop or your supplier.
- Higher Costs:
- Using the incorrect tooling will add to the cost of the project.
- Incorrect tooling could reduce tooling life requiring additional tooling.
- Incorrect tooling can potentially put abnormal strain on the grinder.
- Quality Compromise:
- Inability to achieve a specified finish.
- If the diamond segments are completely gone, the tool holder will damage the floor.
Diamond Tooling Maintenance
- Visual Inspection
- After each tool change, determine how they are performing.
- At the end of each project, remove all damaged tools.
- At the end of the project, separate them by measured segment height. You do not want tools that have different segment heights running at the same time.
- During the project, determine if the tools are wearing evenly. If the tools on one side have worn more than others, the head on the grinder might be bent.
- Proper Storage/Handling
- Clean all tools well before storing them.
- Avoid damage during transportation.
- Label each container with the tooling type.
- Separate wet-only tools from dry-only tools.
Conclusion
Having the correct tooling, in good condition, will make the job run smoothly. During the mock-up phase, select the tooling that will best produce the intended results. Without advanced planning, everyone will become frustrated if the tools are not performing as needed and the time spent on the job will increase.
Tooling is an expensive consumable. When making your tooling decisions, we recommend consulting with your DiamaPro Systems Dealer. They have a wide selection of diamond tooling to choose from. They place a strong emphasis on quality and longevity for all demanding applications.