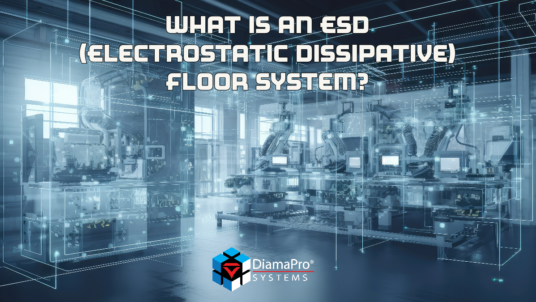
ESD is a phenomenon where static electricity builds up as people walk and then discharges when they touch another object, which can damage electronics or other sensitive components. ESD flooring has conductive elements, such as carbon, graphite, metal-coated particles, or other conductive materials, that create an electrical pathway from the surface to the grounding point. ESD flooring standards depend on the combination of the flooring and the footwear. The electrical resistance of ESD flooring ranges from 2.5 x 104 to 1.0 x 109 Ohms. Ohms is a measurement of electrical resistance. The lower the value, the less resistance there is. ESD flooring is suitable for workplaces with computers, electronics, and larger-scale electronics systems.
Controlling electrostatic discharge begins with understanding how an electrostatic charge occurs in the first place. An electrical charging process begins with a charge that is generated by the contact and separation of two surfaces. These surfaces can be in the form of solids, liquids, or particles, such as gasses, dust, or powder.
What Is ESD Flooring & How Does It Work?
ESD Flooring is designed to reduce or eliminate the potential of electrostatic discharge damaging sensitive electronic components during or after they have been manufactured. The flooring system serves as a conduit for the electrical static charge to discharge to a desired controlled grounding point. Conductive elements within the flooring system provide ESD floors electrical conductivity and create an electrical pathway from the walking surface to the ground. The electrostatic charge that occurs during contact and separation (walking) must be discharged through a grounding point in the floor to move static electricity effectively away from sensitive parts and equipment.
What are the Risks?
If ESD protection and control is not taken into consideration:
- Electrical components could be damaged or destroyed in places where there are electrostatic-sensitive devices.
- It is this potentially unseen, unfelt, or unheard ‘micro lightning’ spark that can occur without warning, which must be prevented or controlled.
- When it comes to flooring, a person who walks over a normal floor stores a negative charge, which may in turn lead to static electroshock. This spark may damage microelectronic parts or even trigger an explosion in the right environment.
Does My Project Need an ESD Floor?
It should always be considered in industries where electronic components or volatile chemicals are involved, static electricity can result in significant damage, injury, and financial loss. All active electronic components and equipment, such as microchips, integrated circuits, and machinery, are sensitive to ESD events. Even when areas and people are equipped to handle such static-sensitive devices, inadvertent contact and damage can still occur.
ESD Testing Basics
Test #1: Electrodes of an industry standard size, weight, and density are placed on the floor at a required distance apart. An electrical charge (voltage) is sent through the Electrodes and with an Ohms meter, measure the resistance between the electrodes in Ohms. Taking readings between two electrodes is referred to as testing the floor's point-to-point (PTP) resistance.
Test #2: Using one of the same weighted electrodes as Test #1, place it on the floor. Connect the other end to the source being used to ground the flooring system. An electrical charge is then sent through the electrode and ground. This is referred to as testing the floor's resistance to ground (RTG).
Note: On most resistance test instruments, the Ohms are expressed as a scientific notation. For example, 1.0E06 (6 zeros with a 1 in front=1million Ohms). An easy way to keep it all straight is the higher the number after the E the HIGHER the RESISTANCE.
Test #3: Place one of the electrodes on the floor and the other in the palm of your hand while standing on the installed ESD floor system in your socks or wearing a set of heel straps in your shoes. This measures Resistance per 97.1 through your body.
Amount of Test Sites
Allow the DiamaPro® ESD Floor System and other systems to fully cure before testing the system for conductivity. All readings must be taken using an instrument such as the Static Solutions, Inc. OHM-STAT® RT-1000. All values taken must be performed during the same time frame. Relative Humidity and Temperature readings must be recorded at the first reading and the last reading.
A minimum of 10 test locations must be provided in areas less than 5,000 square feet. Areas between 5,000-25,000 square feet must have a minimum of 20 test locations. Over 25,000 square feet one test location every 5,000 square feet with a minimum of 20 used.
At every test location, the floor and test apparatus must be clean and dust-free. Follow the cleaning procedures supplied with your test equipment.
Types of ESD Flooring
Static Dissipative: This is an ESD floor with a PTP and RTG tested value greater than 1.0E06 and less than 1.0E09 ohms. Static dissipative flooring is manufactured via two different methods. Either the flooring material is loaded with conductive fibers OR the material, such as DiamaPro® Diama-ESD is manufactured without the conductive additives but with "hygroscopic" capabilities. These hygroscopic capabilities allow the flooring to absorb the ambient humidity in the environment or moisture from the substrate thus rendering the material slightly conductive. Static Dissipative flooring that contains conductive fibers typically falls in the range of 1.0E06 to 1.0E07 and is not reliant on humidity for its static dissipative properties. Hygroscopic materials typically fall in the range of 5.5E07 to slightly less than 1.0E09 ohms at greater than 50% relative humidity.
Static Conductive: These floors have a PTP and RTG tested value of greater than 1.0E04 and less than 1.0E06 (1 Megohm). For electronic manufacturing and other sophisticated static control environments, static conductive is the industry's preferred choice. Why? The combined resistance of drag chains, chairs, carts, and personnel in conjunction with the flooring must be below 1.0E09 (1 Giga-ohm) for compliance with the stringent new standards used in electronics. It's much easier to achieve this with a floor that starts out in the static conductive range. A static conductive floor has about the same resistance as an ESD wrist strap.
High Conductivity: This is a flooring material with a resistance below 1.0E04. It does not meet the industry-accepted safety standards with a minimum electrical resistance of greater than 1.0E04. These flooring materials will eliminate the static charge too quickly for electronic manufacturing. This material is recommended for use by trained personnel ONLY and it is typically only used in specialty Military and munitions applications.
The most popular ranges of electrical resistance for ESD Flooring are Static Conductive and Static Dissipative.
Maintenance
All static control flooring requires cleaning and maintenance. The frequency with which they must be cleaned is dependent on the amount of traffic, the cleanliness of the facility, and the type of service that the product will encounter daily. The following general guidelines will cover most applications where a hard surface ESD system has been installed. Now, the frequency of the procedures may be modified to suit the environmental conditions your flooring may encounter but the process will be the same.
General: Whenever possible, use walk-off mats at entrances and doorways to help reduce the number of abrasives from dirt and grit that enter the protected area. Wire clippings, metal shavings, nuts, bolts, sanding abrasives, etc. can get ground into all types of flooring by foot traffic, and chair casters and may cause scratches. With this type of traffic, DiamaPro® Systems recommends the use of Titanium 40220 HSB conductive chair mats to protect the flooring. Metal chair casters and wheels are not recommended for use with ESD flooring. Nylon or soft rubber ESD chair casters and wheels are acceptable but must be kept clean and free of embedded debris.
Initial Move-In: Protect your ESD flooring investment during the initial move-in phase. Cover the newly installed ESD flooring with brown construction paper or similar materials prior to rolling over the new substrate with heavily loaded pallet jacks, man lifts, etc. Remove nuts, bolts, rocks, nails, etc. from the wheels of heavy equipment prior to rolling over the flooring. The initial installation of the system had a uniform, continuous film. During the move-in step, the floor must remain the same to ensure proper performance.
Note: Concrete/Terrazzo substrates should be vacuumed on a regular basis to remove dirt and dust particulates that may accumulate between seams, cracks, expansion joints, and saw cuts.
Daily: Initially use only new soft bristle brooms and dry dust mops labeled as such. Isolate these tools and use them ONLY on your newly installed ESD flooring. Do not allow them to contact oils, grease, or other contaminants that may be transferred to the ESD flooring. Sweep the area using a broom followed by dust mopping. DO NOT USE ANY TYPE OF SWEEPING COMPOUND.
Weekly: Sweep the area using a broom followed by dust mopping. Damp Mop the flooring with a diluted solution of DiamaPro® Diama-ESD Clean and water to remove abrasives. For use in weekly damp mopping, use a diluted solution of 8-10 ounces of DiamaPro® Diama-ESD Clean per gallon of warm water. Using a clean high-quality mop and a mop bucket with a ringer, dip the mop into the bucket and ring out excess. Rinse the mop in fresh solution often and exchange the dirty damp mopping solution with clean solution as needed. DiamaPro® Diama-ESD Clean may also be used in auto scrubber applications fitted with a soft white pad by adding 8-10 ounces to every gallon of water. After application allow the floor to dry thoroughly. Do not rinse. For heavier soil conditions: Dilute 12 -16 ounces of cleaner per gallon of warm water and use as a mopping solution.
Refinishing
DiamaPro® Diama-ESD Shine is an ESD floor spray buff solution formulated to be used with a high-speed electric or propane powdered burnisher when refinishing DiamaPro® Diama-ESD System is necessary. Light scratching and heavy foot traffic can dull the surface. This proprietary formula is enhanced with special lubricants to reduce overheating while burnishing. DiamaPro® Diama-ESD Shine provides a high luster and a mirror like finish to not only DiamaPro® Diama-ESD System but to all types of hard ESD flooring surfaces including ESD tiles, ESD Sheet vinyl, ESD floor paint and ESD Epoxy/Urethane systems.
Note: Never use plain water to damp mop an ESD floor. The minerals in the water left behind after cleaning could alter the ESD system’s performance.
Average Cost
The cost of ESD flooring varies depending on the type of flooring you are selecting. Typical installed cost is $4.00-$9.00 per square foot. Here are some examples of ESD flooring material costs:
- ESD Tiles starting at $5.00 / sq.ft.
- Epoxy Paint starting at $2.00 / sq.ft.
- ESD Hygroscopic Acrylic starting at $1.00 / sq.ft.
- ESD Carpet starting at $3.50 / sq.ft.
Conclusion
If you are in the market for a solution to meet the ESD requirements of your project, you have many choices. You can select between carpet, VCT, or epoxy systems. If cost is an issue and your floor will only be submitted to light to medium foot traffic, DiamaPro® Diama-ESD is well suited for your project.
DiamaPro® Diama-ESD is an easy, low-cost solution to many ESD flooring needs. The system uses very low V.O.C. waterborne technology that can be installed in any U.S. market. It’s a complete system with a sealer, finish coat, grounding tape, and cleaning solution. If you have any questions regarding ESD floor coatings or Diama-ESD, reach out to DiamaPro Systems and ask for our coatings specialist!