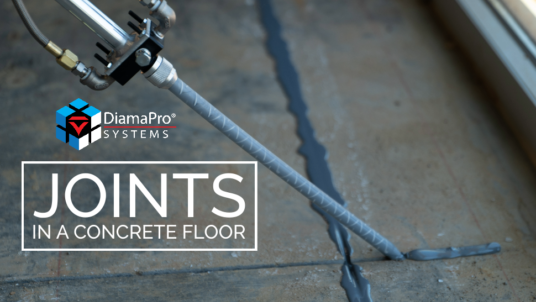
However, concrete will move, and it shrinks during the curing process. It expands and contracts when in an environment that has temperature changes, and when connected to an area that moves in different ways. This is where joints are installed in concrete to prevent cracking in the slab where you don’t want them.
Joint Types
Several types of joints are installed in a concrete slab based on their function. The function of the joint also dictates the type of joint filler that should be used.
Construction joints: Joints that separate different sections of concrete poured at different times. They are also called “Cold Joints” describing a joint placed butted up next to a cured, hard slab. A construction joint is also used in cases of equipment breakdown during concrete placement, an unexpected shortage of concrete, or bad weather popping up during a pour that needs to be stopped and continued later.
If the slab has no significant traffic crossing the joint, a nonreinforced butt joint is acceptable. If there’s expected traffic other than foot traffic, you will need a way to transfer loads over the joint from the existing slab to the new slab.
Expansion joints: Concrete is extremely stiff and doesn’t contain any elasticity. You may think concrete is so hard that it doesn’t move, but that’s not the case. It’s not a forgiving material. Expansion and contraction pressure inside the concrete builds as the temperature changes. This pressure relieves itself by cracking in another area of the slab. If a joint was there, it could have absorbed pressure and possibly prevented the crack. This is why expansion joints are used.
Expansion joints create a break between concrete slabs and other rigid parts of a structure. Concrete expands and contracts as it changes temperature. It can also shift with the movement of the earth. Concrete expansion joints give the slab room to move which helps prevent cracks & buckling. Without expansion joints, movement could create pressure and stress which eventually causes unwanted defects. Expansion joints are a stress relief to relieve pressure and prevent damage.
Contraction joints: A contraction joint or control joint is a saw cut in the slab. Using the cut as a weak point, we try to force the shrinkage crack that develops while the concrete is curing to follow it. We are creating a weakened line (joint) in the slab where we want it and let nature take its course and hope it cracks within the joint.
After concrete is placed, it is going to shrink. We can reduce shrinkage with good mix designs, but it is always going to shrink, and we need to accommodate it. Contraction joints are formed by saw cutting, hand-tooling with a grooving tool, or inserting a plastic strip into the concrete during finishing. Proper timing and depth of the cut are essential. If you wait too long, the slab will crack where it wants to rather than where you want it to. If the joint is not cut deep enough, it will not create the plane of weakness needed to guide the crack.
Saw cuts can be made with conventional wet-cut or dry-cut saws or with an early-entry saw.
Using an early-entry saw, cuts can be made within 1 to 4 hours which is much earlier than with a conventional saw. The saw-cut is typically 1 inch deep regardless of slab thickness—although even ¾-inch deep early-entry cuts can function properly.
Conventional wet-cut concrete saws can be used to cut joints, typically waiting until the concrete achieves a strength of about 500 psi to prevent the raveling of the cut edges during sawing. The timing varies depending on the temperature and the relative humidity, but the window is generally 4 to 12 hours after concrete placement. The cut depth should be at least 25% of the thickness of the slab.
The jointing pattern may or may not be specified on every project. For an unreinforced slab, control joints should be spaced in feet 2 to 3 times the slab thickness in inches. For a 4-inch slab, space the joints 8 to 12 feet apart. Jointed panels should be as square as possible. Keep the length divided by the width of a panel (aspect ratio) no more than 1.5 (so if the panel is 12 feet long it should be no less than 8 feet wide). Avoid L- and T-shaped panels and the cuts should be straight and continuous, never staggered.
Isolation joints: An isolation joint is the separation of an existing concrete slab from a new concrete slab or wall. With a wall, a piece of expansion joint (usually fiber material) is placed against the existing wall and when the new concrete slab is poured next to it, this expansion joint separates the two allowing for movement.
There are times when base pads are installed that support columns holding up the roof system or machine isolation pads separating the machine vibration from the main floor while providing much additional support. In both scenarios, the concrete pad is much thicker than the floor. They can be anywhere from 1’ to 6’ thick depending on the intended use. The joint separating the floor from the pad is used to eliminate any load or vibration transfer into the floor.
Joint Filler
With the numerous joints that can be found on a normal concrete floor, there will be many open voids that will collect dirt and harbor harmful microbes. Forklift traffic also has an impact on the service life of the floor while driving over open control joints.
Construction, isolation, and expansion joints are all considered to be dynamic (moving) joints. They need to be able to move. The joint filler used should have enough movement capability to satisfy the amount of joint movement it will be subjected to. A typical joint sealant for these joint types falls in the polyurethane family. Polyurethanes have high movement capabilities ranging from +-25% to +- 50%. Usually the higher the movement capabilities, the softer the polyurethane filler will be once cured. They are installed to keep the joint clean and waterproof.
Contraction (control) joints are considered stable and will not move as much as the other three. But they will still move. Filling them with a ridged material will only lead to joint filler failure or slab cracking next to the joint. A semi-ridged polyurea joint filler such as DiamaPro Diama-Joint will not only keep them cleaner but will allow forklifts to roll over them without depressing into the joint minimizing joint shoulder impact. It creates a bridge within the joint. Control joint filler is hard but with some flexibility. The joint is filled full depth to the bottom of the joint providing support to the filler. When the filler is shaved level with the concrete surface, forklifts can roll across the joint without impacting the joint shoulders. This minimizes joint shoulder deterioration.
Conclusion
There is more than one type of concrete joint. They all have their use and must be filled with the appropriate joint filler. They reduce slab cracking, allow slab movement, and direct shrinkage cracks to a predetermined location. When you are on the next job, let’s see if you can determine what types of joints you’re looking at, and if are they filled with the correct joint filler. As always, if you need assistance choosing a joint filler, joint saw, or even determining what you are looking at, contact DiamaPro Systems for help!