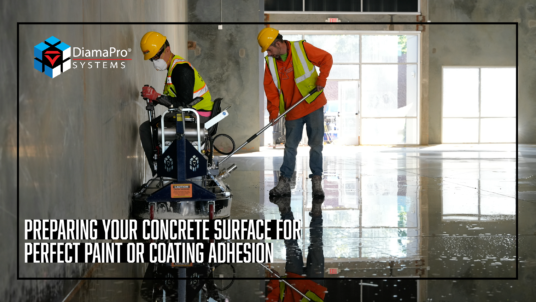
Lack of surface preparation is the number one cause of failure in concrete paint, coatings, and toppings. Every system has an optimum surface profile (texture) required to develop the best bond. To obtain the correct surface profile for the system being installed, a means to mechanically prepare the surface will be needed. The rougher the required surface profile, the more aggressive the mechanical preparation will be.
A thin mil paint or resinous coating will require less of a profile than a heavy, thick cement-based mortar. The thin systems will normally suggest a less aggressive texture because a rough profile will reflect through the cured coating and be visually unacceptable.
It is always recommended to consult with the manufacturer of the paint or coating when determining the correct surface profile. They have performed numerous tests on their materials to help you select the optimal process of how to prepare the concrete floor for paint or coating application.
Why is Surface Preparation Important
Paints and coatings adhere only mechanically to the substrate. The surface preparation process is the most important step during the installation. You can purchase the best, most expensive paint or coating on the market, but without preparing the substrate correctly, the system will most likely fail at the bond line.
Assessing Your Concrete Surface
No two concrete substrates are the same. Before the surface preparation step starts, you must assess what you will be working on. Having cracks, spalls, and stains becomes a constant battle. There are not many existing concrete floors that will not have some type of defect.
Having the appropriate repair material for the defect type is crucial. Fine cracks and small chips can be filled with neat (no added aggregate) DiamaPro Diama-Grout, a low-viscosity, urethane resin. This material is very thin to promote great absorption and fast setting to minimize downtime. Medium size spalls, up to 6” in diameter and 2” in depth, can be filled with DiamaPro Diama-Grout mixed with oven-dried sand or pea gravel. The sand and pea gravel need to be completely dry, and free of all water. This can be purchased along with the Diama-Grout at a local construction material supplier.
Most concrete slabs will have joints or saw cuts. These saw cuts were installed within 24 hours after the concrete was placed to minimize shrinkage cracks. When concrete cures, it will shrink. Joints are cut into the slab as weak plains to direct the cracking within the joint. These joints need to be filled. DiamaPro Diama-Joint is a polyurea joint filler. It sets fast to minimize downtime. It not only fills the joint, but it also fills it with a material that will aid in transferring wheel loads over the joint. This helps minimize wheel impact on the joint shoulders.
Without addressing these joints or defects before applying the paint or coating, they will reflect through the cured film leaving an unacceptable appearance.
Concrete Hardness: The concrete hardness will determine the metal bond tooling to use during the grinding process. The diamonds in the metal bond tooling are secured to the tool with a metal alloy. When grinding, the metal wears away to expose new, fresh diamonds. The rate the metal wears away is based on the concrete hardness and the metal hardness. To efficiently grind hard concrete, you want to use a soft metal alloy. To grind soft concrete, you will use a hard metal alloy.
Concrete hardness is determined with the use of a Mohs Hardness kit. A Mohs hardness test kit is a set of 8 picks with different hardness values (2-9) that are used to determine the surface hardness. The test is simple but not exact. When testing the hardness of the concrete surface, it will get you in the hardness ballpark to select the metal bond tooling to start with.
Moh's Hardness | Concrete Hardness | Metal Bond Tooling |
---|---|---|
2-3 | Soft Concrete | Hard Bond for Soft Concrete |
3-5 | Medium Concrete | Medium Bond for Medium Concrete |
5-7 | Hard Concrete | Soft Bond for Hard Concrete |
8-9 | Extra Hard Concrete | Very Soft Bond for Extra Hard Concrete |
Before testing the hardness, make sure there are no sealers or curing compounds on the surface. Film-forming materials will impact the results and must be removed to obtain accurate hardness values.
Gathering the Necessary Tools and Materials
Safety must be a focus when starting a project like this. Quality gloves, protective eyewear, dust masks, and leather boots are tools of the trade. It can be hot in the summer but wearing a long sleeve shirt and long pants will reduce minor injuries.
When repairing concrete, you will need to prepare the defect or joint to obtain a bond. Hand grinders and concrete saws are the tools most contractors will use. Anytime dust is generated, a dust extractor needs to be used to reduce harmful airborne particulates.
There are 3 mechanical methods used to prepare a horizontal concrete surface. Shotblast, grind, and scarify. When applying a thin mil paint or coating, grinding or shot blasting is used.
A concrete grinder is easy to control. They come in different sizes so choose one that fits the size of your project. A commercial dust extractor is connected to the grinder capturing concrete dust. The tooling that is cutting comes in different grits. Very similar to sandpaper but the industrial diamonds are held to the tool base with metal.
Shotblasting is another method that can be used. The same dust extractor used when grinding must be used when blasting. A shot blaster propels metal shot (BBs) to the ground, leaving a rough, clean surface. The level of roughness is based on the concrete hardness, power of the shot blaster, speed of travel, and the shot size. With paint or coating, a light to medium blast is all you need. A 110-volt 8” path shot blaster can perform the work. 280-330 shot size is a good place to start. The machine travel speed should be set to the medium range to start. Caution needs to be taken if the operator has minimal experience running a shotblaster. If the machine is stopped while the blast wheel is still throwing shot to the ground, a huge, deep rut will be cut into the concrete.
Equipment Availability
Both grinder and shotblaster are readily available for rent or purchase. If renting, Sunbelt Rentals is a very good place to start. Their technicians do provide training on all their equipment. Niagara Machine, Inc. will be the place to purchase. They have several offices throughout the country with a very knowledgeable sales staff that will also provide training.
How to Prep Concrete for Paint or Coating: A Complete Guide
Diamond Selection
The Mohs Hardness Kit determines the hardness of the concrete surface. Using the tested value, select the appropriate 30-grit metal bond tool.
Diamond tools have cutting segments. They could be round, star, or bar-shaped. There will also be 1 or 2 or 3 segments on each tool. The lighter the grinder weighs, the fewer segments you will want. The fewer segments, the more pressure it will exert on the floor. With a lightweight grinder, you want less surface area on each tool.
Grinder
- Cut the floor with 30-grit metal bond diamonds.
- 2nd cut - Cut with the same 30-grit diamond parallel to the first cut.
- Vacuum the floor removing all debris from the chips, cracks, spalls, and joints.
Concrete Repair
- Fill all medium-sized spalls with Diama-Grout / oven-dried aggregate blend.
- Overfill all the small chips and cracks with DiamaPro Diama-Grout.
- Overfill all joints with DiamaPro Diama-Joint.
- When cured (1 hour) shave the joint material level to the joint shoulders.
Grinder
- Cut the floor with a 70-grit metal bond diamond.
- If the floor has been fully processed (cut evenly) you can vacuum to accept the paint or coating.
- If the floor has not been fully processed, cut again perpendicular to the previous cut with the 70-grit metal bond diamond.
Auto-scrub
Some paint and coating manufacturers require an auto scrub before application. An auto-scrubber is a ride-on or walk-behind machine that injects clean water into the floor, scrubs it with a rotary brush, then extracts the dirty water with a squeegee from the floor. If you are to use an auto-scrubber, allow the floor to fully dry before application.
Conclusion:
The most important step in prepping a concrete floor for paint or coating is proper surface preparation. If not performed correctly, the service life of your new floor will be shortened.
With the selection of the appropriate equipment, the surface preparation process will go smoothly and not be time-consuming. The size of the equipment will be dictated by the size of the project. A small piece of equipment is much easier to move around but the production rate might be extended, slowing down the project.
The paint or coating manufacturer should have a printed recommendation on how to prepare the floor and what the surface needs to be. If they are not willing to supply you with this information, we recommend looking for another material supplier. As always, if you need any assistance learning how to prep a floor for paint or coating, you can contact DiamaPro Systems for equipment, accessories, coating, and expertise!